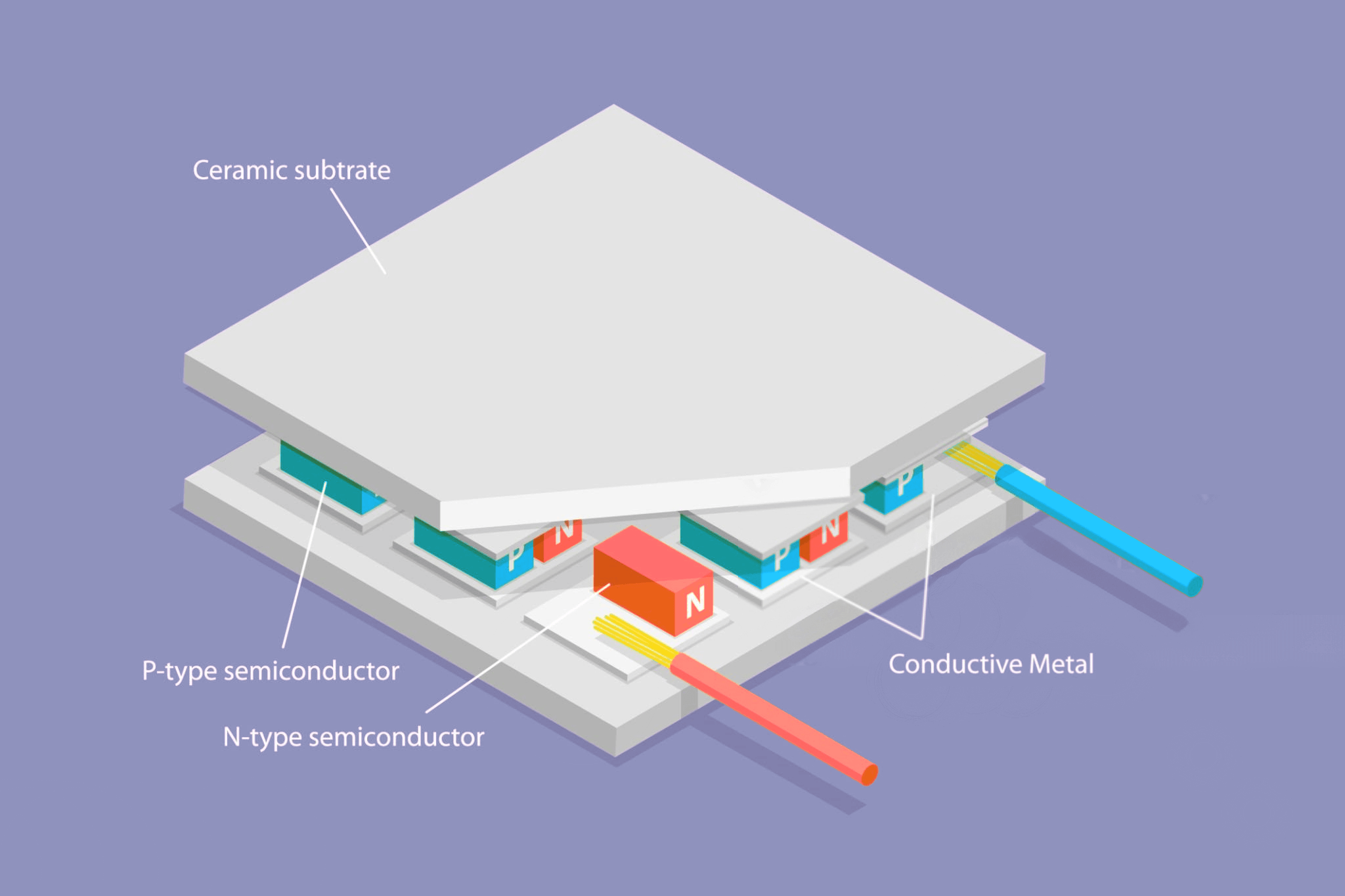
The semiconductor industry is continuously evolving, with environmental sustainability and space efficiency driving innovation. Among the technologies making significant strides is thermoelectric temperature control—a solid-state solution that combines rapid, precise thermal management with refrigerant-free operation.
Basics of Thermoelectric Technology
A thermoelectric (TE) module, commonly referred to as a Peltier device, is a solid-state assembly that leverages the Peltier effect to manage heat. It consists of an array of Bismuth Telluride semiconductor pellets that have been “doped” so that one type of charge carrier, either positive or negative, carries the majority of current. The pairs of P/N pellets are positioned between two metalized ceramic plates. These plates provide the platform for the pellets and the small conductive tabs that connect them. The pellets, tabs and substrates thus form a layered configuration. When a direct current is applied, charge carriers migrate across junctions, transferring heat from one side to the other. The “cold side” absorbs thermal energy for localized cooling, while the “hot side” dissipates it. By reversing the voltage polarity, the roles of the hot and cold sides can be switched, enabling the same device to function for both heating and cooling applications.
Understanding Thermoelectric Temperature Control Units (TCUs)
In semiconductor manufacturing, TCUs are typically configured by electrically connecting P-type and N-type elements in series while arranging them in parallel for thermal conduction (see diagram below). In this arrangement, often referred to as a “couple,” the cold side of the TCU is directly attached to a heat-generating component to absorb heat, while the hot side is coupled to a heat sink or liquid-cooled plate to dissipate it.
Unlike conventional refrigeration systems that depend on mechanical compressors and chemical refrigerants, thermoelectric TCUs transfer heat via the movement of charge carriers. This solid-state approach reduces mechanical complexity and minimizes failure risks. Moreover, when multiple Peltier devices are integrated, the overall cooling (or heating) capacity scales linearly with the applied current. Because these TCUs are installed in close proximity to the heat source, thermal lag is minimized, enabling rapid response and enhanced temperature stability—attributes that are critical for sensitive semiconductor processes.
Why Semiconductor Manufacturers Are Turning to Thermoelectric Cooling
As global regulations tighten (for example, with the Kigali Amendment phasing down hydrofluorocarbons), semiconductor fabs are increasingly prioritizing environmentally friendly cooling solutions. Thermoelectric TCUs provide a fully refrigerant-free alternative, making them ideal in scenarios where traditional heat exchangers are impractical.
These systems excel in dynamic temperature control. By varying the applied current, thermoelectric systems can quickly adjust their cooling power, allowing them to respond promptly to sudden heat load changes while maintaining optimal process conditions.
Additionally, thermoelectric cooling units are notably more compact than traditional compressor-based systems, as they lack bulky refrigeration components. This compactness allows for more flexible installation options and conserves valuable space in cleanroom fabs or subfabs.
The Future of Semiconductor Cooling: Thermoelectric Solutions
Thermoelectric technology presents a compelling solution for the semiconductor industry. By delivering precise, reliable, and environmentally friendly temperature control, thermoelectric TCUs help address the challenges of energy efficiency and spatial constraints.
For instance, the LAUDA SEMISTAT thermoelectric process thermostat—built on proven Peltier technology—provides rapid and accurate thermal management while consuming up to 90% less energy than conventional systems. Its refrigerant-free design and compact 2.5L fluid reservoir contribute to lower operating costs and reduced environmental impact.
In applications where precise temperature control is critical, thermoelectric solutions like the LAUDA SEMISTAT offer a robust, efficient, and sustainable approach tailored to the needs of semiconductor manufacturing.
This post was authored by Tom Fiaoni, Semiconductor Industry Specialist at LAUDA-Brinkmann.