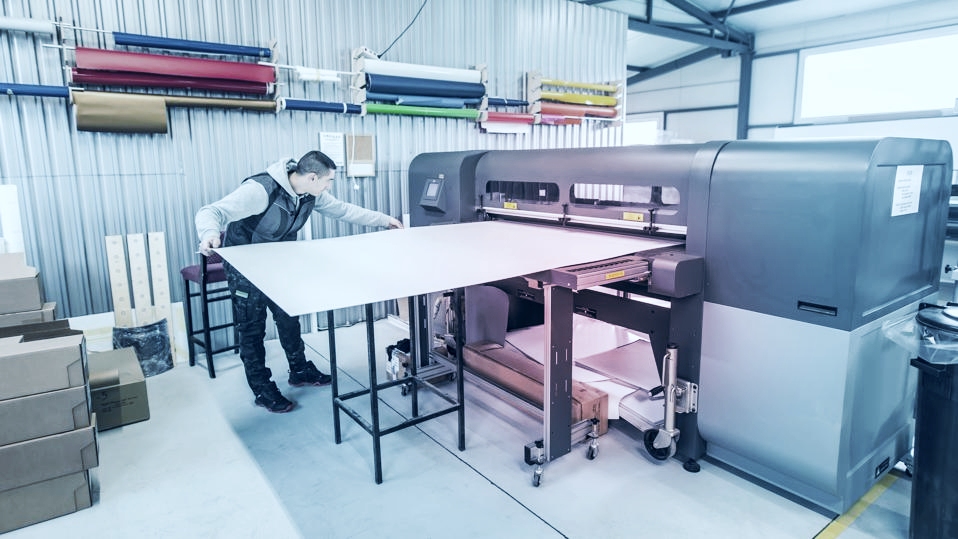
In digital printing presses, effective thermal management is critical to maintaining optimal performance and ensuring high-quality print outputs. These systems generate substantial heat through various processes, making precise temperature control essential to prevent quality issues and equipment degradation.
One of the primary sources of heat is electrophotographic printing, a widely used technique that involves multiple stages of energy-intensive operations. The process begins with a photoconductive drum receiving an electrical charge, followed by selective laser exposure to create an electrostatic image. Toner particles then adhere to the charged regions before being fused onto paper using heat and pressure—often reaching temperatures as high as 200°C. This final fusing step significantly contributes to the internal thermal load of the printing system.
Beyond electrophotography, mechanical operations also generate heat. High-speed rollers, motors, and gears introduce friction, elevating the temperature of both the machinery and the materials being printed. If not properly managed, this excess heat can affect ink viscosity and substrate stability, potentially leading to print defects and reduced operational efficiency.
Additionally, many modern digital printing methods, including inkjet and UV-curable printing, rely on drying and curing processes that further contribute to thermal buildup. Inkjet printers often use heated air or infrared radiation to evaporate solvents, accelerating the drying process. UV-curable printers employ ultraviolet light to cure inks instantly, adding another heat source to the press environment. When these factors combine, uncontrolled thermal conditions can lead to misaligned colors, substrate warping, and increased mechanical wear, ultimately affecting both print quality and equipment lifespan.
To mitigate these thermal challenges, advanced cooling solutions are essential. One effective approach is centralized cooling systems, which distribute chilled water or coolant from a central unit to multiple press components. This method helps regulate overall pressroom temperatures, reducing the risk of localized overheating and ensuring a stable operating environment.
Another widely used solution is recirculating chillers, which operate in a closed-loop system to absorb and dissipate heat from critical press components. By circulating a coolant—typically water or a water-glycol mixture—these systems maintain precise temperature control, which is essential for consistent print quality and long-term equipment reliability. Recirculating chillers are particularly effective in removing excess heat from electrophotographic processes, mechanical operations, and UV curing systems, preventing thermal fluctuations that could compromise production efficiency.
Maintaining stable thermal conditions in digital printing is essential for consistent print quality, reduced maintenance, and prolonged equipment lifespan. Without proper cooling, excessive heat can lead to print defects, substrate deformation, and unplanned downtime.
The LAUDA Ultracool series provides a reliable and energy-efficient solution for managing thermal loads in digital printing. These chillers offer precise temperature control, with a temperature range of -10 to 35°C and ±0.5 K stability, ensuring consistent process conditions across various printing applications. Designed with energy efficiency in mind, Ultracool chillers use variable-speed compressors and intelligent temperature regulation to optimize power consumption, reducing energy costs by up to 50%, depending on operating conditions.
In addition to performance and efficiency, remote monitoring capabilities allow for real-time adjustments, enabling operators to proactively manage thermal conditions and prevent overheating. With these advanced features, LAUDA Ultracool chillers provide an ideal cooling solution for digital printing operations that require precise temperature regulation, reliability, and cost-effective energy use.