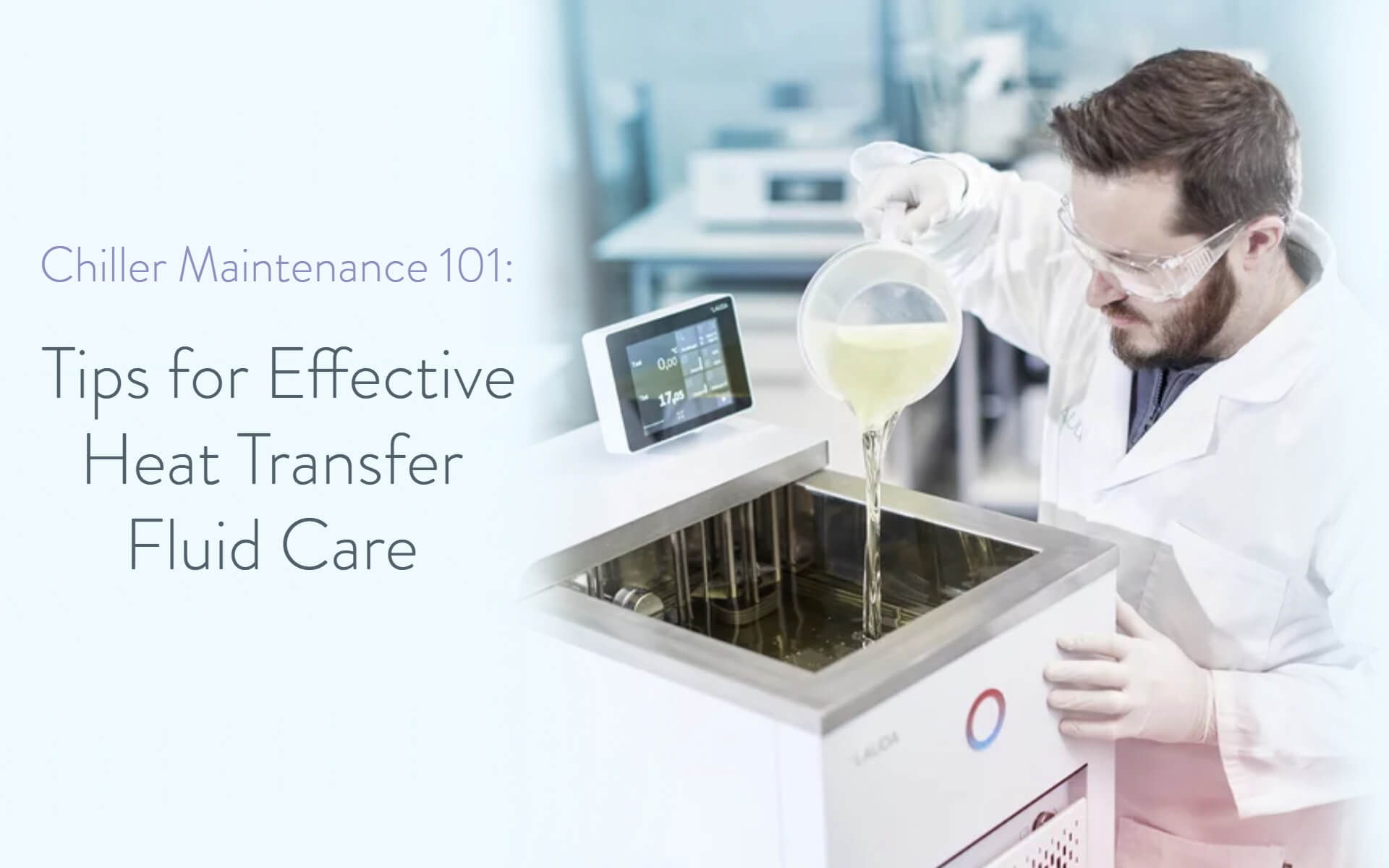
Why Change Your Heat Transfer Fluid?
Regularly changing your heat transfer fluid is crucial for maintaining your chiller’s performance and reliability. Over time, the fluid degrades due to factors like temperature fluctuations, oxidation, organic growth, and contamination. This degradation can lead to reduced thermal efficiency, blockages in the system, and potential damage to key components.
Failing to replace the fluid on schedule can result in the buildup of sludge, particulates, and other deposits that clog internal passages, reduce heat transfer, and strain the pump or compressor. Over time, this neglect can drastically shorten the lifespan of your chiller, leading to costly repairs and unexpected downtime.
When Should You Change the Fluid?
While the frequency of fluid changes can vary depending on the type of fluid used and the process conditions, there are several key indicators to help you determine the optimal time for replacement. Below, are some guidelines to know when it is best to change your fluid:
Fluid Appearance and Smell
A visual inspection is often one of the easiest ways to determine if your fluid needs to be replaced. Fresh fluid is typically clean and free from particulates, but as it degrades, it can become discolored, murky, or develop suspended particles. The presence of sludge or sediment at the bottom of your fluid tank is another red flag, indicating that the fluid is no longer performing as it should.
Additionally, odor can be a strong indicator of fluid degradation. Heat transfer fluids, especially those that are oil-based or glycol-based—such as the fluids we provide at LAUDA—, can produce a noticeable smell when they begin to break down. If you detect an unusual or “burnt” smell, it’s a clear sign that the fluid has oxidized or overheated and should be replaced immediately. The formation of acids, from oxidative degradation, can also corrode internal components, causing further issues if not addressed promptly.
Operating Temperatures
The temperatures at which your system operates have a significant impact on the longevity of your heat transfer fluid. Processes that maintain temperatures near ambient (room temperature) typically experience slower fluid degradation, allowing for less frequent changes. However, extreme temperatures, especially at the high end of a fluid’s rated range, can cause rapid breakdown. Operating above the fluid’s recommended temperature will lead to scorching, which permanently alters the chemical composition and performance of the fluid.
Silicone oils, for example, are commonly used for high-temperature processes but are susceptible to thermal cracking if exposed to excessive heat for long periods. This results in lower viscosity, increased volatility, and poor heat transfer efficiency. On the other hand, water-glycol mixtures, often used in mid-range temperatures, can experience changes in concentration when exposed to heat. Water tends to evaporate, leaving behind a more concentrated glycol solution that may impact the fluid’s ability to circulate effectively and cool or heat the system properly.
Glycol Concentration
For water-glycol mixtures, maintaining the proper concentration is vital to both the effectiveness of heat transfer and the longevity of your system’s components. Over time, the water component of the mixture may evaporate, especially if the system is operating at high temperatures or under vacuum conditions. This leaves behind a higher concentration of glycol, which can be detrimental to both the pump and the heat transfer performance.
Using a glycol concentration gauge is a simple, cost-effective way to monitor the fluid’s concentration. These gauges measure the refractive index, giving you a quick and accurate reading of the water-to-glycol ratio. Maintaining this ratio within the manufacturer’s recommended range ensures that the fluid continues to flow smoothly through the system without causing excessive wear on the pump seals or internal piping. Frequent checks are recommended if your system experiences temperature swings, and adjustments to the concentration may be necessary depending on your operating conditions.
Contamination Risks
Contamination of the heat transfer fluid can occur in several ways, particularly if your system uses quick-connect fittings or is exposed to an environment where external particles can enter the fluid loop. Frequent disconnection of hoses or the presence of dust, dirt, or other debris in the work environment can introduce contaminants that compromise the fluid’s performance.
To reduce contamination risks, ensure that your system is sealed as much as possible, and avoid frequent fluid exposure to the surrounding environment. If contaminants do enter the system, they can accelerate the degradation of the fluid and may even clog the system’s internal components, such as heat exchangers, resulting in reduced cooling or heating capacity. In extreme cases, the entire system may need to be flushed and cleaned to restore performance. Always inspect hoses, seals, and connections for wear and tear that might allow contaminants to enter.
Idle Time
Chillers that sit idle for extended periods are at risk of fluid degradation due to stagnation. When the system is not running, and the fluid is not circulating, it can provide an ideal environment for the growth of microorganisms, such as algae or bacteria, especially in water-based fluids. Even though LAUDA fluids contain inhibitors designed to slow the growth of such organisms, these additives have a finite lifespan and may become less effective over time.
Before restarting a chiller that has been idle for several weeks or months, inspect the fluid for any signs of discoloration, cloudiness, or unusual odor. If the fluid appears compromised, it’s best to replace it before resuming normal operation to prevent contamination of the system and maintain optimal performance.
Unexpected Situations
There are times when unusual circumstances may require you to inspect the fluid, even outside of your regular maintenance schedule. If you notice any changes in the system’s performance—such as inconsistent temperatures, longer cycle times, or reduced cooling capacity—it’s worth checking the condition of your heat transfer fluid.
Faulty or degraded fluid can cause a range of issues, including poor heat exchange, cavitation, and increased wear on pumps and compressors. Ignoring these signs can lead to more severe system failures, requiring costly repairs or part replacements. If there’s any doubt about the fluid’s condition, it’s better to err on the side of caution and perform a replacement.
LAUDA’s Recommendation
As a general rule, LAUDA recommends changing your heat transfer fluid at least once a year, regardless of fluid type or process conditions. Over time, even the most stable fluids will degrade due to chemical and thermal stress. By changing the fluid annually, you ensure that your system continues to operate at peak efficiency, minimizing the risk of downtime and costly repairs. Regular fluid changes help prevent the buildup of harmful contaminants, avoid the degradation of critical system components, and maintain the thermal stability necessary for precise temperature control.
In conclusion, staying proactive with your fluid maintenance schedule is a small investment that yields long-term benefits for your chiller’s performance and reliability.
This post was authored by Justin Caruso, Inside West Sales Manager at LAUDA-Brinkmann.