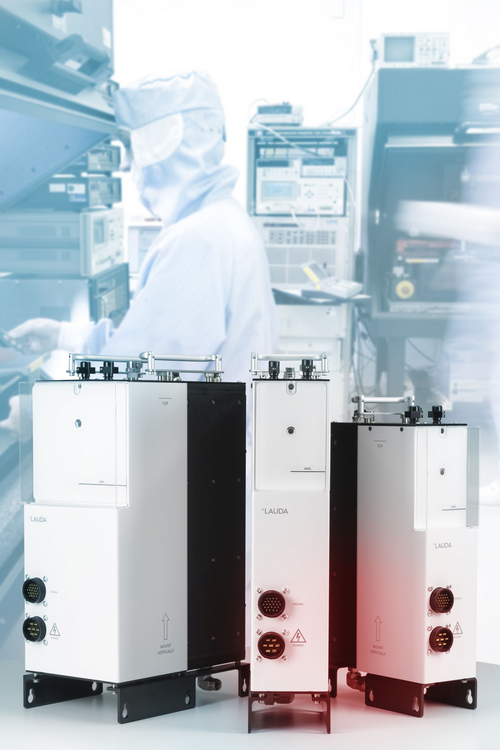
Process Details
- Process: Oxide Etch
- RF Power: 3.6kW (combined upper & lower electrode)
- Target Temperature (T Set-point): 20 °C at the lower electrode
- Chiller Comparison: OEM qualified compressor-based chiller vs. LAUDA-Noah POU system
Data Acquisition System Setup Our data acquisition equipment configuration adheres to standard industry practices. We have meticulously recorded the supply and return fluid temperatures within the lower electrode cooling loop at the specific request of the customer. Additionally, we have extended our data collection to encompass temperature readings from the TEL ESC (wafer) and integrated this information with the LAUDA-Noah Data Acquisition System (DAQ).
Contact Etch Process Recipe Information
Step Name | Step # | Step Time | RF Lower | RF Upper |
---|---|---|---|---|
Stab | 1 | 14/60 | 0 | 0 |
Breakthrough | 2 | 20 | 800 | 1500 |
Stab | 3 | 8/60 | 0 | 0 |
Main Etch | 4 | 130 | 1800 | 1800 |
Stab | 5 | 6/60 | 0 | 0 |
Over-etch | 6 | 10 | 100 | 1000 |
Stab | 7 | 4/60 | 0 | 0 |
Dechuck | 8 | 17 | 100 | 1000 |
Pump | 9 | 2 | 0 | 0 |
211 Seconds or ~3 minutes
Application & Challenges The customer encountered a series of critical issues:
- Substantial 1st wafer effect and through-the-lot temperature rise stemming from RF-induced temperature drifts exceeding 8 °C in TEL Unity IIe SCCM chambers with the OEM qualified chiller.
- Frequent temperature alarms when operating the OEM qualified chiller at the desired 20 °C set-point, prompting the customer to run the process at 25 °C.
- Consideration of a switch back to 20 °C and the inclusion of recipe cool-down time for the OEM qualified chiller, although this would adversely affect chamber and tool throughput.
- The continuous display of 20 °C on the chiller’s front panel throughout processing, despite performance issues.
Evaluation of the LAUDA-Noah POU Solution
Our evaluation encompassed two primary aspects:
1. Ramp Rate Comparison (Cooling Efficiency):
- The LAUDA-Noah POU system exhibited a remarkable 489% faster ramp-up, completing in just 1.7 minutes, compared to the OEM chiller’s 9.0 minutes.
- For ramp-down, the LAUDA-Noah POU system was 175% faster, with a 3.3-minute duration, while the OEM chiller took 5.7 minutes.
2. Through-the-Lot Temperature Profile Comparisons (25 Wafer Lots):
- Utilizing ESC RTD readings from the tool’s software, we captured temperature data that further revealed the performance discrepancy.
- The LAUDA-Noah Data Acquisition System (DAQ) monitored supply and return fluid temperatures, confirming the advantages of Dynamic Temperature Control.
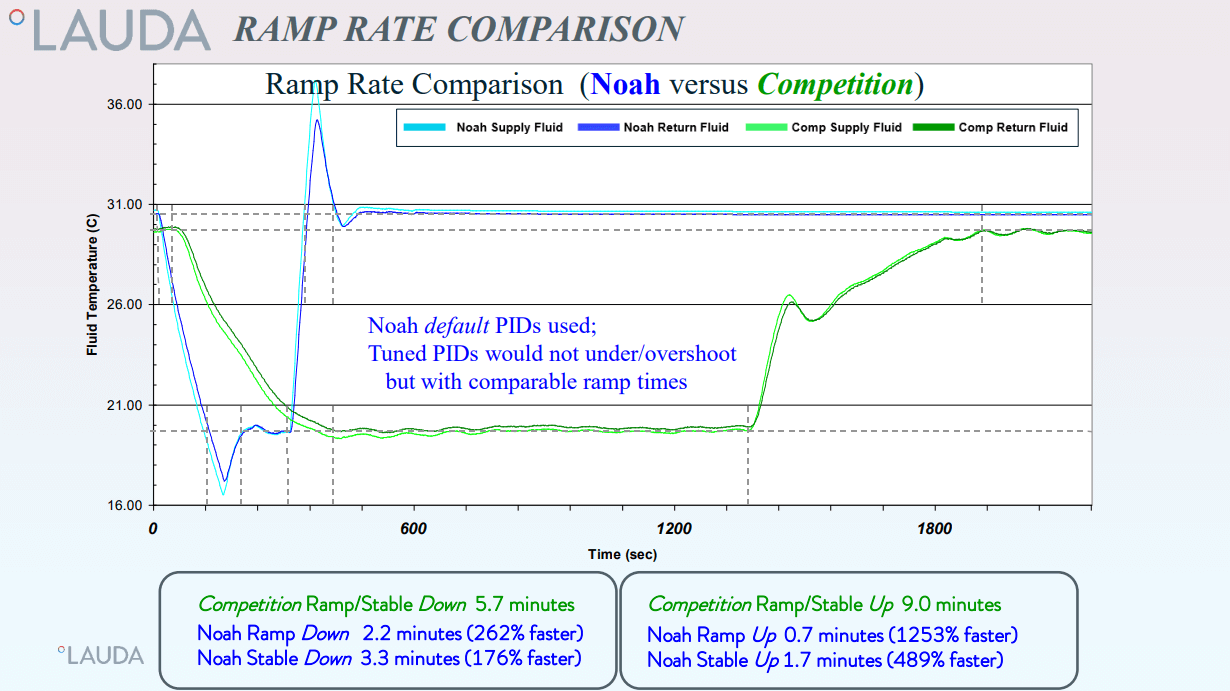
Temperature Profile Comparisons The temperature profiles provided valuable insights. During a production run, we observed an approximate 2 °C fluid temperature rise per wafer, resulting in an overall temperature increase through-the-lot. This had been a consistent challenge faced by the customer since the installation of the tool, with the OEM qualified chiller erroneously reporting a ~20 °C temperature throughout the process, as shown in the supply fluid temperature.
In a subsequent data set collected under identical conditions, we noted significant improvements in temperature uniformity. It is crucial to emphasize that this data set employed the LAUDA-Noah controller with its DEFAULT P.I.D. settings. Remarkably, even with factory settings, the LAUDA-Noah POU system succeeded in reducing the overall temperature variance per wafer by more than 50%.
Technical Comparison
- OEM Qualified Chiller:
- Cooling capacity: 2.5kW
- Season/dummy wafers run prior to LOT (1st wafer effect ~4 °C temp. rise during seasons not shown)
- 2.1 °C rise of initial wafer temperature post-seasoning
- 1/5 °C rise of final wafer temperatures post-seasoning
- ESC temperature average through-the-lot exceeds 27 °C
- Process temperature set-point is 25 °C
- OEM qualified chiller erroneously reads 20 °C through LOT processing.
- LAUDA-Noah POU Chiller:
- Cooling capacity: 1.2kW @ 20 °C
- No seasoning dummy wafers run prior to this Noah lot
- < 2.0 °C rise of initial wafer temperatures
- ~2.0 °C rise of final wafer temperatures
- Noah system closely adheres to the original target set-point of 20 °C.
In conclusion, the LAUDA-Noah POU system’s advanced Dynamic Temperature Control offers superior performance, with faster ramp rates and enhanced temperature uniformity. It resolves critical challenges related to RF-induced temperature drifts and ensures precise temperature control, making it an ideal choice for temperature-sensitive processes in semiconductor manufacturing.