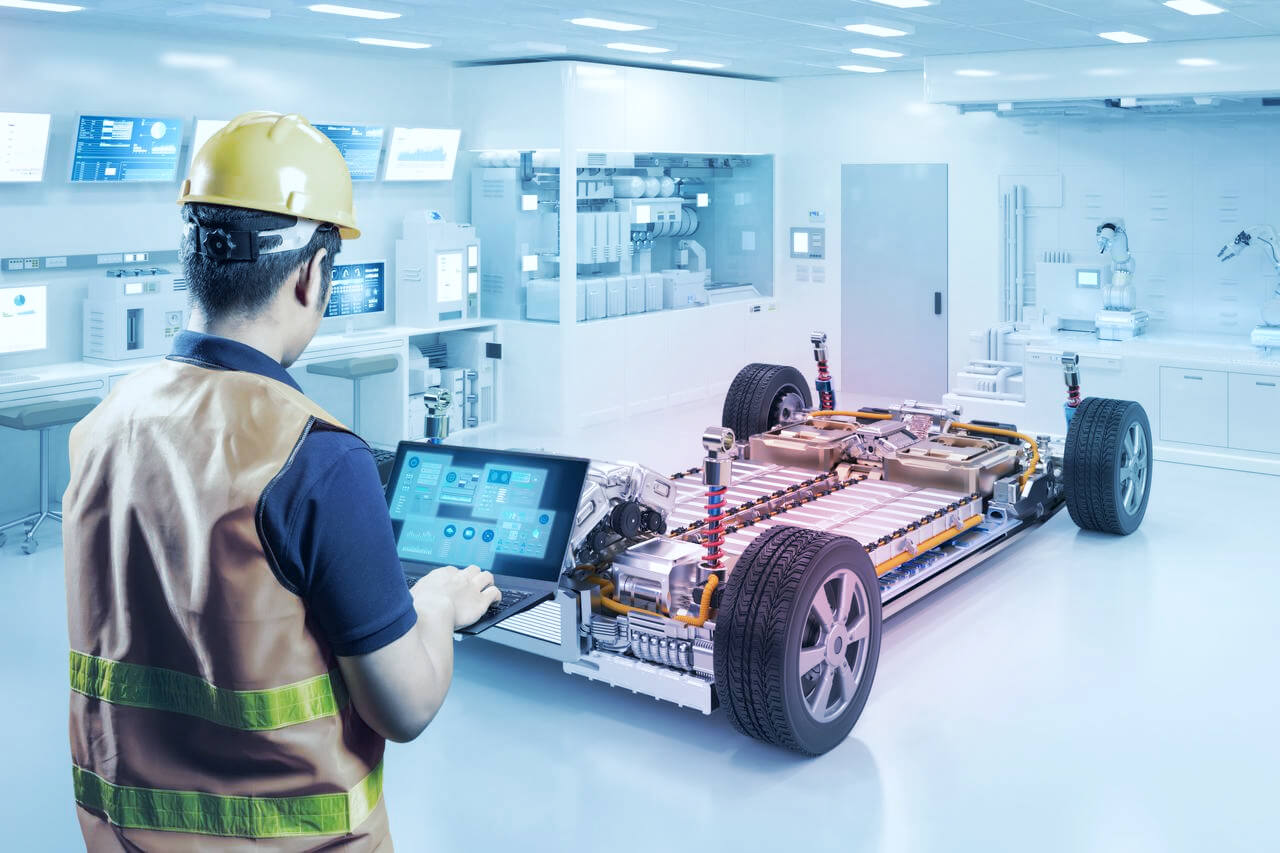
The Importance of Temperature Control in EV Battery Testing
As the world rapidly shifts towards electric vehicles (EVs), the need for reliable and efficient battery testing solutions has never been more critical. Understanding the intricacies of EV battery testing is essential for ensuring the safety, reliability, and performance of these vehicles.
One of the key factors in EV battery testing is precise temperature control. Battery testing involves subjecting the battery cells or packs to various stress conditions, including high and low temperatures, to simulate real-world operating environments and a battery cycler to replicate charging and the use of the battery.. The thermal management during these tests is critical because temperature variations can significantly impact battery performance, safety, and lifespan. During the testing process, batteries generate significant heat due to the electrochemical reactions occurring within the cells. Effective heat management is essential to prevent overheating, which can lead to thermal runaway, a dangerous condition where the battery’s temperature rapidly increases, potentially causing fires or explosions.
Our advanced chiller units are designed to provide precise temperature control using a glycol-water mixture with a temperature range of -40°C to 100°C. This capability is important for managing the heat generated during battery testing and maintaining stable temperatures throughout the process. By ensuring that batteries operate within their optimal temperature ranges, we can accurately assess their performance, efficiency, and durability.
Cell-Level Testing
During cell-level testing, individual battery cells are placed on cooling plates inside an environmental chamber. This type of testing focuses on evaluating the performance and characteristics of individual cells, which are the building blocks of larger battery packs. The environmental chamber is equipped with sensors and control systems to precisely monitor and adjust the temperature, humidity, and other environmental conditions. While the Battery cycler is applying a charge or discharging the cells being tested.
Our chiller units are connected to these cooling plates to regulate the temperature accurately. The environmental chamber simulates real-world operating conditions, such as extreme temperatures and rapid temperature changes, allowing for the identification of potential issues early in the development process. This helps in optimizing cell design and chemistry before scaling up to full battery packs.
Complete Battery Pack Testing
For comprehensive battery pack testing, the entire pack is placed inside an environmental chamber. Battery packs consist of multiple cells arranged in series and parallel configurations to achieve the desired voltage and capacity. Testing at the pack level is crucial to ensure that all components, including cells, connectors, and cooling systems, function harmoniously under various conditions.
Our chillers are connected to the pack’s inlet and outlet, replicating the function of a car’s radiator system. This setup ensures thorough testing of the battery pack under various temperature conditions, ranging from -65°C to 180°C. These extreme conditions are used to evaluate the pack’s thermal management system, electrical performance, and mechanical integrity. By simulating different operational scenarios for battery use as well as charging, we can identify potential failure points and optimize the design for better safety and reliability.
Enhancing Safety and Efficiency
The precise temperature regulation provided by our chillers enhances the safety and efficiency of the battery testing process. By maintaining stable temperatures, our units help prevent overheating and ensure consistent test results, contributing to the overall reliability of EV batteries. Temperature stability is particularly important for assessing battery degradation over time, as even slight temperature fluctuations can accelerate wear and reduce lifespan.
In addition to preventing overheating, our chillers help in identifying and mitigating thermal imbalances within the battery pack. Thermal imbalances can lead to uneven aging of cells, reducing the overall efficiency and capacity of the battery. By ensuring uniform temperature distribution, we enhance the pack’s performance and longevity.
At Lauda Brinkman, we believe in working closely with our customers to understand their unique challenges and requirements. We are committed to providing solutions that meet the evolving needs of the automotive industry.
This post was authored by Zach Myers, Automotive Industry Specialist at LAUDA-Brinkmann.